案例|上海竹園污泥干化焚燒工藝設(shè)計
發(fā)布時間:2017/01/23 點擊量:
1 總體設(shè)計
本工程主要包括污泥接收和儲運系統(tǒng)、污泥干化系統(tǒng)、污泥焚燒系統(tǒng)、余熱利用系統(tǒng)、煙氣處理系統(tǒng)、公輔系統(tǒng)等,主體工藝流程見圖1。
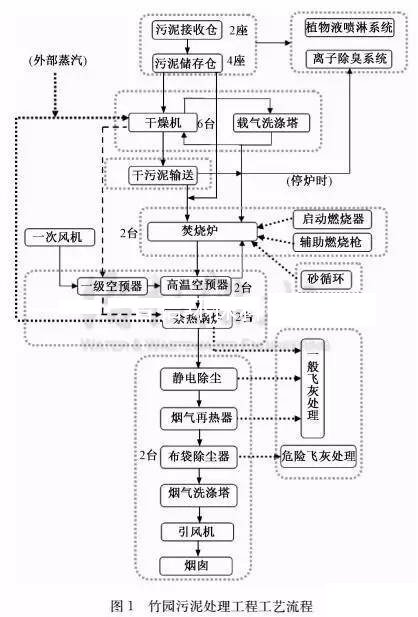
2 污泥接收儲運系統(tǒng)
4座污水處理廠的脫水污泥通過卡車運輸至本污泥處理廠區(qū),經(jīng)物流出入口的地磅稱重計量后,卸載至4座地下污泥接收倉,每倉有效容積30m³。污泥由接收倉底部的4臺柱塞泵分別輸送至4座污泥儲倉,儲倉總有效容積1500m³,可儲存2天進廠污泥量。儲倉下共設(shè)8臺污泥輸送泵,其中6臺螺桿泵與6臺干化機一一對應(yīng)供泥,2臺液壓柱塞泵將剩余部分濕污泥直接輸送至焚燒爐前的混合進料螺旋。
3 污泥干化系統(tǒng)
本工程共配置了6臺四軸槳葉式干化機,單臺換熱面積為200m²。槳葉式干化機適用于高粘度物料的干化,它能夠直接跨越污泥粘滯區(qū),產(chǎn)出含固率60%以上的干污泥,便于采用皮帶、螺旋等簡單的方式進行輸送。槳葉采用了特殊的齒合設(shè)計,葉片之間具有自清潔功能,防止污泥在受熱面板結(jié)影響傳熱效率。國內(nèi)污泥含砂量高,對設(shè)備磨損嚴重,因此對槳葉進行了100%碳化鎢耐磨噴涂。
在干化機空心軸、槳葉和夾套中通入0.5~0.8MPa飽和蒸汽,濕污泥從干化機一端進入,在干化機內(nèi)以推流形式緩慢前進并逐漸被干化和破碎,最后半干污泥從另一端排出。干化機內(nèi)通過循環(huán)載氣(空氣)將機內(nèi)水分快速帶走,同時保證干化機內(nèi)部處于微負壓狀態(tài)。排出的濕載氣溫度在85~90℃,經(jīng)過洗滌塔洗滌降溫至40~50℃并脫除水分后,80%送回干化機循環(huán)使用,剩余20%送入焚燒爐作為焚燒二次風(fēng),同時載氣中有機成分被高溫分解脫除臭味。采用直接洗滌方式,洗滌水采用污水處理廠處理尾水,冷凝液排放至污水池后經(jīng)提升返回污水處理廠處理。
干化熱源主要來自余熱鍋爐產(chǎn)生的蒸汽,不足部分引入外高橋發(fā)電廠的蒸汽。外高橋蒸汽用量取決于污泥的含水率和熱值。冷凝水經(jīng)換熱器降溫后,進入除氧器除氧后返回鍋爐系統(tǒng)。
4 污泥焚燒系統(tǒng)
焚燒爐是整個工程的核心。本工程設(shè)置2臺鼓泡流化床焚燒爐,每臺焚燒爐直徑7.3m(外徑),高度14.8m,立式圓柱鋼殼體,內(nèi)有耐火材料及保溫材料襯里,外設(shè)保溫夾套,每臺焚燒爐額定熱負荷12.35MW。焚燒爐自下而上依次為錐底、流化區(qū)、自由燃燒區(qū)。焚燒爐布風(fēng)采用布風(fēng)管形式,設(shè)于砂床下部,布風(fēng)管向下開孔,通過焚燒爐錐形底部的反射作用將砂床流化。每臺焚燒爐床層上部設(shè)置兩套啟動燃燒器用于焚燒爐啟動時升溫,每套負荷12000MJ/h,使用輕柴油作為燃料;底部設(shè)有輔助燃燒系統(tǒng),每臺焚燒爐設(shè)8個噴油槍,用于運行中爐溫的調(diào)節(jié)。焚燒爐頂部設(shè)有冷卻水噴槍和噴尿素系統(tǒng),用于防止焚燒爐超溫和減少氮氧化物產(chǎn)生。
干化后含水率40%以下的污泥經(jīng)皮帶機和鏈板機輸送和提升,再經(jīng)螺旋分配至4個干污泥緩存?zhèn)},每個緩存?zhèn)}容量12m³。緩存?zhèn)}下設(shè)置計量槽對干污泥進行稱重后,進入焚燒爐前的混合進料螺旋,與剩余含水率80%左右的濕污泥混合后進入焚燒爐焚燒,混合污泥含水率為60%左右。污泥進入流化床后被劇烈擾動狀態(tài)的灼熱床料打磨、迅速破碎并均勻分布到砂床內(nèi),并與空氣充分接觸,實現(xiàn)污泥穩(wěn)定和完全燃燒。砂床靜止時厚度約1.5m,流化時厚度約2.5m,石英砂平均粒徑在0.3~0.5mm。設(shè)有砂循環(huán)系統(tǒng),根據(jù)砂床高度和床砂品質(zhì)的變化進行補砂或換砂操作,一般不需排渣,熱損失較少。
焚燒爐設(shè)一次和二次供風(fēng)系統(tǒng)。設(shè)置2臺一次流化風(fēng)機,配置能力16744Nm³/h每臺,出口風(fēng)壓35kPa,額定工況單臺焚燒爐供風(fēng)量12150Nm³/h。一次風(fēng)包括全廠收集的臭氣和焚燒爐夾套中抽吸的熱空氣,首先經(jīng)過一級空氣預(yù)熱器與干化機蒸汽凝結(jié)水換熱,將溫度升高至80℃左右,再經(jīng)過焚燒爐出口煙道上的二級高溫空氣預(yù)熱器,與焚燒產(chǎn)生的熱煙氣換熱,溫度升高至300℃左右,從砂床下部的布風(fēng)管進入。二次風(fēng)來自干化機循環(huán)載氣,直接通入焚燒爐自由燃燒區(qū),確保完全燃燒,額定工況風(fēng)量3075Nm³/h。
與一般焚燒系統(tǒng)設(shè)計相比,本工程焚燒系統(tǒng)設(shè)計有如下特點:
(1)鼓泡流化床焚燒爐是目前污泥焚燒使用最多的形式,其最大的特點是底部的流化砂床有著相當(dāng)大的熱容量,最適用于像污泥這種低熱值、高含水率、性質(zhì)波動大、且難以引燃和燃盡的低品質(zhì)燃料的燃燒。能夠?qū)崿F(xiàn)污泥自持燃燒,當(dāng)供泥穩(wěn)定時焚燒爐不需要添加輔助燃料。
(2)布風(fēng)管和反射錐設(shè)計形式簡單、維修更換方便,焚燒爐內(nèi)部無活動部件,既保證了砂床的流動均勻性及合理的粒徑分布,又避免了對布風(fēng)裝置的磨損和堵塞,爐渣和結(jié)塊也容易從爐底排出。
(3)焚燒爐外部設(shè)置了夾套,通過抽吸夾套中的熱空氣作為一次風(fēng),然后利用干化冷凝水余熱對一次風(fēng)進行預(yù)熱,高效利用能源的同時確保焚燒爐表面溫度滿足低于50℃的規(guī)范要求。
(4)全廠的設(shè)施設(shè)備通過臭氣收集系統(tǒng)的抽吸形成負壓,防止臭味擴散。臭氣作為一次供風(fēng),部分干化不凝氣作為二次供風(fēng),通過高溫焚燒的方式實現(xiàn)高效除臭。
(5)污泥采用后混方式入爐,相對于不后混的方式,可以避免污泥含水率在粘滯區(qū)附近造成輸送困難的情況,同時可以通過干濕污泥配比的調(diào)節(jié),靈活應(yīng)對污泥含水率波動和熱值季節(jié)性的變化,實現(xiàn)污泥自持燃燒和節(jié)能。
5 余熱利用
焚燒煙氣經(jīng)過高溫空氣換熱器后溫度變?yōu)?60℃左右,然后進入余熱鍋爐。設(shè)置2臺余熱鍋爐,每臺蒸汽產(chǎn)量8 t/h,將污泥焚燒煙氣中的熱量轉(zhuǎn)化為壓力8bar(1bar=0.1MPa)、溫度175℃的飽和蒸汽,供干化使用??紤]到流化床焚燒煙氣中含塵量較高的特點,余熱鍋爐采用單鍋筒膜式水冷壁形式,設(shè)置蒸汽吹灰器,在保證高效的同時具有初步降塵的作用。余熱鍋爐出口煙氣溫度降低至260℃左右,熱能得到有效利用。
6 煙氣處理系統(tǒng)
本工程配套2條煙氣處理線,余熱鍋爐出口的煙氣依次通過靜電除塵器、布袋除塵器、洗滌塔并經(jīng)再熱器后達標排放。
煙氣首先進入靜電除塵器,可去除95%以上的飛灰。靜電除塵器收集的飛灰通過氣力輸送至飛灰倉,加濕后作為一般固體廢物外運處置或利用。
在袋式除塵器前的煙氣管道中噴入粉末活性炭,用于吸附煙氣中的Hg等重金屬以及二惡英等有機化合物?;钚蕴恐刑砑邮乙远杌钚蕴糠乐蛊淙紵捅?,混合比例1∶10。布袋除塵器捕集的飛灰通過氣力輸送至廢料倉,作為危險廢棄物,委托專業(yè)單位外運處置。
經(jīng)袋式除塵器處理后的煙氣進入煙氣洗滌塔下部,先進行脫酸處理。采用NaOH作為吸收劑,吸收煙氣中的HCl、SOx等酸性氣體。塔內(nèi)設(shè)有填料,洗滌液由泵循環(huán)。脫酸后的煙氣進入洗滌塔上段,進一步降溫和除濕。
為防止煙氣排放時產(chǎn)生白煙,設(shè)計了煙氣再熱工藝。經(jīng)靜電除塵器處理后的煙氣進入煙氣再熱器,與洗滌后的冷煙氣換熱,熱煙氣溫度由226℃降至170℃,然后進入布袋除塵器。而冷煙氣則從50℃提升至105℃以上后高空排放,煙囪高度50m。
本工程設(shè)有煙氣在線監(jiān)測系統(tǒng)(CEMS),對煙氣流量、溫度、壓力、濕度、氧濃度、煙塵、氯化氫(HCL)、二氧化硫(SO2)、氮氧化物(NOx)、一氧化碳(CO)、氟化氫(HF)和二氧化碳(CO2)等參數(shù)進行實時監(jiān)測和控制,檢測結(jié)果同時上傳政府環(huán)保監(jiān)管平臺。
7 主要工藝控制
干化系統(tǒng)主要控制污泥干化量和污泥干度兩個參數(shù)。通過干化機進泥管道上設(shè)置的電磁流量計反饋信號變頻控制污泥螺桿泵,實現(xiàn)濕污泥給料速率的控制。出泥干度通過升降干化機出口處的堰板,以調(diào)整污泥在干化機內(nèi)的停留時間來實現(xiàn)。干化機尾部設(shè)有溫度探頭,當(dāng)內(nèi)部溫度超過160℃時,自動噴水降溫以保證干化系統(tǒng)運行安全。載氣風(fēng)機使干化機內(nèi)形成-(100~500Pa)微負壓,微負壓控制通過壓力探頭反饋信號,自動調(diào)節(jié)載氣風(fēng)機出口返回干化機和至焚燒爐兩條分支管路上的電動調(diào)節(jié)閥開度實現(xiàn)。
焚燒爐正常運行時自由燃燒區(qū)溫度控制在850~900℃,當(dāng)爐溫低于850℃時,啟動底部的輔助油槍系統(tǒng);當(dāng)溫度超過900℃時,啟動頂部噴水設(shè)施。焚燒爐不同高度設(shè)有6個溫度探頭,爐溫檢測信號反饋至中控溫度自動控制模塊,通過計算給出干、濕污泥投加速率和比例,實現(xiàn)爐溫自動調(diào)節(jié),使污泥在一定的溫度波動范圍內(nèi)自持燃燒。焚燒爐的濕污泥給料控制通過變頻污泥泵來實現(xiàn),干污泥給料量通過計量槽下部變頻螺旋來控制。額定工況下每臺焚燒爐干污泥給料量設(shè)定值為4.646t/h,濕污泥給料量設(shè)定值為4.306t/h。焚燒爐出口煙氣氧含量控制在6%~10%,通過調(diào)節(jié)一次風(fēng)機進口擋板來調(diào)節(jié)一次風(fēng)量,實現(xiàn)過??諝饴士刂?。焚燒爐正常運行時通過上述3T+E技術(shù),即燃燒溫度、停留時間、混合程度、過??諝饴实目刂疲瑏韺崿F(xiàn)穩(wěn)定燃燒和減少污染物排放。
爐內(nèi)壓力通過壓力儀表反饋和引風(fēng)機變頻器控制電機轉(zhuǎn)速進行,維持在-(0.5~1.0)kPa微負壓狀態(tài)。當(dāng)爐頂壓力超過2 kPa后,急排煙囪自動開啟。
通過儀表檢測洗滌液pH自動調(diào)節(jié)NaOH投加量。洗滌液pH一般設(shè)定在7左右??筛鶕?jù)煙氣在線監(jiān)測儀表反饋數(shù)據(jù),調(diào)整洗滌液pH,確保煙氣排放中的二氧化硫等酸性污染物指標在安全范圍內(nèi)。